When tackling a sand blasting project, selecting the right equipment is essential for achieving the desired results. Sand blasting is a versatile process used for surface cleaning, preparation, and finishing. Whether you’re removing rust, paint, or other debris, choosing the correct sand blasting equipment ensures efficiency and high-quality outcomes.
For projects in Malaysia, understanding your options, including the use of glass blasting beads and other abrasives, can make a significant difference in your results.
Why Sand Blasting Matters for Your Project?
Sand blasting is a surface treatment method used across various industries in Malaysia. This propelling on a high speed abrasive material cleans or etches a surface. Depending on your project’s needs, you can choose from different blasting abrasives, such as glass blasting beads or sand, which have varying levels of aggressiveness.
Your choice of equipment determines your finishing, durability, safety, and best of all. Whether you’re working on metal, concrete, or even wood, sand blasting helps you prepare surfaces to achieve superior bonding or a clean appearance.
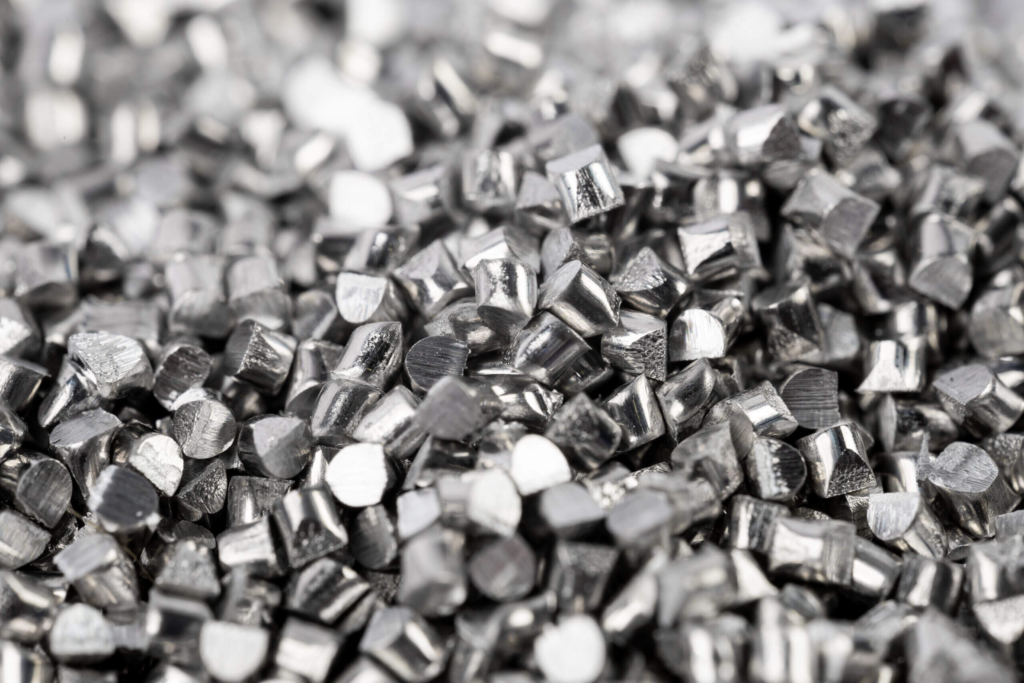
Types of Sand Blasting Equipment
Different sand blasting projects require different types of equipment. The type of material you are working with and the type of finish you seek will all play a role on which equipment will be suitable. Here are the main types of sand blasting equipment commonly used:
- Pressure Blasters
High-performance, large-scale projects should be ideal for pressure blasters. They push abrasive materials like sand or glass blasting beads under high pressure. These types of equipment are ideal to clean big metal parts, remove rust, or make the surface rough in order to perform a coating process.
- Suction Blasters
Suction blasters are more suited for small projects or for jobs that need more delicate work. These are the type of machines that draw the abradable materials into the air stream so they are ideal for smaller, finer surfaces. If you are working on automotive parts or sculptures, a suction blaster with glass blasting beads could be the perfect choice.
- Blasting Cabinets
Closed blasting cabinets are used to contain the dust and let you blast small parts to hold the mess. Specifically speaking, these are really handy for projects where precision is demanded. Cleaning component that requires its integrity to be maintained is done well by blasting cabinets. You can also use glass blasting beads in these cabinets to get a finer, more even finish.
Understanding Glass Blasting Beads vs. Sand Abrasives
Two common abrasives used in sand blasting are traditional sand and glass blasting beads. Every one of these materials has its own benefits as compared to your project needs. For reference, here is quick comparison:
Glass Blasting Beads:
Glass blasting beads are a more refined, gentle abrasive. These are shaped like spheres permitting smoother and a more controlled blast. Therefore, they are perfect for getting some(last minute) cleaning or finishing, while you still keep the surface in tact.
Glass blasting beads are perfect for:
- Etching glass or metals
- Removing the final trace of obscurity from sensitive parts without leaving behind roughness.
- Achieving a smooth, satin finish
Sand Abrasives:
More traditional sand abrasives are also cheaper but can be more aggressive. Sand has an angular shape that is sharper than rounded marbles, which helps it remove heavier contaminants such as rust and old paint quickly. But sand can also wear more on the surface leaving a rougher finish.
- Aggressive rust and paint removal well suited for use.
- Works well on larger surfaces
- Good for those projects in need of heavy cleaning.

When to Choose Glass Blasting Beads?
If your project requires a finer, smoother finish, glass blasting beads are the better choice. As an example, these beads prevent the metal component from being scratched or damaged when being cleaned where the surface must remain smooth and undamaged.
When to Choose Sand Abrasives?
Sand abrasives give you the advantage when you’ve got to remove thick coatings, rust or other stubborn materials. Sand is also more economical if you are working on large surfaces. Just not suitable for delicate work where the surface damage is a concern.
Key Considerations When Choosing Sand Blasting Equipment
When choosing sand blasting equipment for your project, keep these factors in mind:
- Project Size and Scope
Pressure blasters will provide the power for you if you are working on a large industrial scale project. For smaller, precision tasks, suction blasters or blasting cabinets with glass blasting beads will give you the control and accuracy required.
- Material Type
Depending on the surface, the abrasive need not be the same. Harder materials like steel may need more aggressive abrasives like sand, while softer surfaces may benefit from glass blasting beads. The material you’re working with determines which abrasive to choose.
- Finish Requirement
For projects where surface finish is crucial, such as when preparing items for coating or painting, glass blasting beads can offer a smoother, more uniform result. Sand abrasives are the ones you want to the use for a rougher, more aggressive finish.
- Budget
The choice of suitable equipment and abrasives depends on the budgets available. While glass blasting beads may be slightly more expensive, they offer better finishes, which can reduce the need for further treatment. Sand abrasives can usually be bought cheaper, but it does require more maintenance on equipment.
Conclude
Where diverse industries rely on sand blasting, understanding the nuances between different abrasives and equipment types can make all the difference. Always go for safety, and don’t use the right tool, the wrong tool.